A Process Calibrator is a specialized instrument used to calibrate temperature, humidity, and other process variables in industrial environments. Accurate calibration is critical for ensuring the performance of measurement instruments, maintaining product quality, and complying with industry standards. In this guide, we will explore the workings of a Process Calibrator, its functions, and why it is essential for industries that require precise environmental measurements.
Table of Contents
- What is a Process Calibrator?
- Basic Principles of a Process Calibrator
- Types of Process Calibrators
- Main Components of a Process Calibrator
- Steps to Operate a Process Calibrator
- How to Choose the Right Process Calibrator?
- Applications of Process Calibrators
- Advantages and Challenges of Process Calibrators
- Conclusion
What is a Process Calibrator
A Process Calibrator is an instrument designed to simulate process conditions and verify or adjust the calibration of sensors, transmitters, and other measurement devices. It ensures that these instruments are providing accurate readings, which is crucial in industries such as aerospace, pharmaceuticals, and manufacturing.
Process calibrators are used to simulate a range of values, such as temperature, pressure, and humidity, so that devices can be calibrated to match these conditions. This process ensures that measurement instruments are reliable and consistent over time.
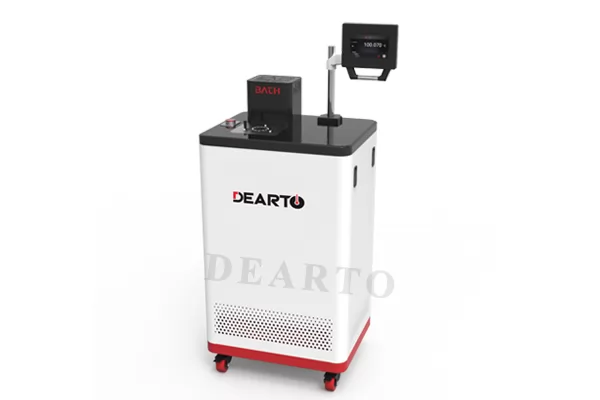
Oil Bath Temperature Calibration
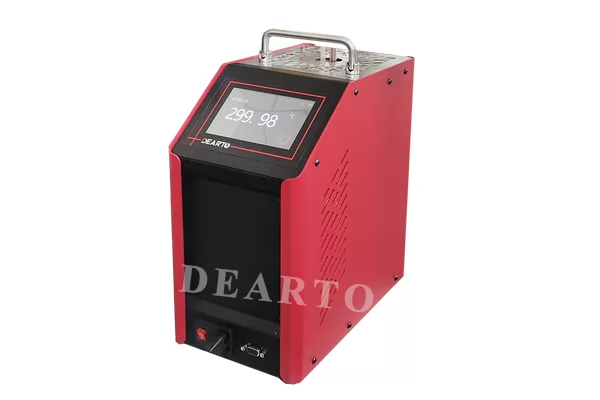
Dry Block Calibrator
Basic Principles of a Process Calibrator
The basic principle behind a Process Calibrator is simple: it generates a standard reference value for a specific process variable (e.g., temperature, pressure, or humidity). The calibrator sends this value to the instrument under test, which adjusts its readings to match the reference.
Process Calibrators work by:
- Generating accurate and stable reference signals.
- Comparing the device's output to the known reference value.
- Adjusting the device's calibration to ensure it meets the required accuracy.
Types of Process Calibrators
There are several types of Process Calibrators, each designed to meet different industry needs. Some of the most common types include:
- Temperature Calibrators: Used to calibrate temperature sensors and instruments.
- Humidity Calibrators: Used to ensure accurate measurement of humidity levels.
- Pressure Calibrators: Designed for calibrating pressure sensors and gauges.
- Multi-parameter Calibrators: These can calibrate multiple parameters (e.g., temperature, humidity, and pressure) simultaneously, offering versatility for complex calibration needs.
DEARTO is committed to innovation, and many of their Process Calibrators incorporate self-calibrating technology, reducing the need for regular manual adjustments and improving operational efficiency.
Main Components of a Process Calibrator
A typical Process Calibrator consists of several key components that work together to generate, measure, and compare process signals:
- Reference Standard: A precise, calibrated reference source.
- Measuring Circuit: The system responsible for comparing the instrument under test with the reference.
- Display/Interface: Provides real-time feedback, showing the calibration results or adjustments.
- Calibration Adjustment Mechanism: Allows for fine-tuning and calibration of the instrument.
Steps to Operate a Process Calibrator
Operating a Process Calibrator typically involves the following steps:
- Select the Process Variable: Choose the parameter to be calibrated (e.g., temperature or humidity).
- Set the Reference Value: Enter the known reference value for the selected variable.
- Connect the Device Under Test: Attach the sensor or instrument to the calibrator.
- Measure and Compare: The calibrator compares the instrument’s output to the reference value.
- Adjust the Calibration: If there’s a discrepancy, adjust the device to match the reference value.
How to Choose the Right Process Calibrator?
Choosing the right Process Calibrator depends on several factors:
- Type of Measurement: Ensure the calibrator is designed for the specific process variable you need (e.g., temperature or pressure).
- Accuracy and Stability: Look for a calibrator that provides high accuracy and stable performance.
- Range of Operation: Ensure the calibrator can handle the range of values required by your instruments.
- Ease of Use: Choose a calibrator with an intuitive interface for ease of operation.
Applications of Process Calibrators
Process Calibrators are used across various industries where accurate measurements are critical. Some common applications include:
- Process Calibrators are used across various industries where accurate measurements are critical. Some common applications include:
- Manufacturing: Ensuring precision in the production of goods, where small deviations can lead to defects.
- Pharmaceuticals: Maintaining strict temperature and humidity controls during drug production and storage.
- Aerospace: Ensuring environmental conditions are met for sensitive equipment.
- Energy and Utilities: Monitoring temperature, pressure, and humidity in power generation facilities.
Advantages and Challenges of Process Calibrators
By regularly calibrating instruments with a Process Calibrator, industries can ensure that their measurement devices provide accurate and reliable data, which is essential for quality control and regulatory compliance.
- Improved Accuracy: By ensuring instruments are calibrated correctly, Process Calibrators help maintain accuracy across systems.
- Regulatory Compliance: Regular calibration ensures compliance with industry standards and regulations.
- Cost Efficiency: Properly calibrated instruments reduce the risk of costly errors and downtime.
Conclusion
A Process Calibrator is a vital tool in ensuring the accuracy of temperature, humidity, and other critical measurements in industrial environments. By maintaining the precision of measuring devices, process calibrators contribute to improved operational efficiency, product quality, and safety.
The future of Process Calibrators lies in the integration of automation and smart technologies. DEARTO is at the forefront of these innovations, offering cutting-edge solutions that help industries stay ahead of the curve in maintaining measurement accuracy and reliability.