Calibration equipment plays a crucial role in ensuring the safety and reliability of aircraft components in the aerospace manufacturing industry. The accuracy and precision of measurements and readings are essential to maintaining the high standards required in the aviation industry. In this article, we will discuss the importance of calibration equipment in aerospace manufacturing, the various types of calibration equipment used, and why calibration is crucial in the aviation industry.
Calibration equipment refers to instruments and devices that are used to ensure that the measurements and readings of other instruments are accurate and precise. In aerospace manufacturing, calibration equipment is used to calibrate measurement instruments such as pressure gauges, torque wrenches, and thermometers, among others. Calibration equipment ensures that these instruments are properly calibrated and accurately measure the parameters they are designed to measure.
|
What is Calibration Equipment?
Calibration equipment includes a wide range of instruments and devices used in aerospace manufacturing. Some of the most common types of calibration equipment used in aerospace manufacturing include:
Calibration software: This type of calibration equipment is used to manage calibration data, track calibration schedules, and generate calibration reports.
Calibration standards: These are reference instruments used to calibrate other instruments. Calibration standards are used to establish the accuracy of measurement instruments and ensure they are properly calibrated.
Calibration systems: These are automated systems used to calibrate instruments automatically. Calibration systems help reduce human error and ensure that instruments are calibrated accurately and consistently.
Calibration processes and methods involve comparing the readings of a measurement instrument with a reference standard of known accuracy. The difference between the reading of the instrument being calibrated and the reference standard is then adjusted to bring the instrument into calibration.
Why is Calibration important?
Calibration is essential in aerospace manufacturing for several reasons:
The purpose of equipment calibration is to ensure that instruments and devices used in aerospace manufacturing produce accurate and precise measurements. This is important for maintaining the safety and reliability of aircraft components.
Importance of calibrated instruments in aerospace manufacturing: Calibrated instruments are essential for maintaining the quality of aerospace components. They ensure that the measurements taken during production are accurate and reliable, which helps reduce the risk of errors and defects in the finished product.
Benefits of calibration in the aviation industry: Calibration provides several benefits to the aviation industry. It helps to improve the accuracy and reliability of measurements, which in turn leads to better-quality products. Calibration also helps reduce the risk of accidents caused by faulty instruments, which can lead to injuries and damage to equipment.
The Role of Calibration Equipment in Aerospace Manufacturing
The importance of calibration equipment in aerospace manufacturing cannot be overstated. Calibrated instruments are essential for maintaining the safety and reliability of aircraft components. Without proper calibration, the measurements taken during production may be inaccurate, which can lead to defects and safety issues in the finished product.
A calibration equipment list is a comprehensive list of all the instruments and devices that require calibration in aerospace manufacturing. Calibration equipment lists are used to ensure that all instruments are properly calibrated and that the calibration process is managed effectively.
Calibration services are also available for aerospace manufacturers. Calibration service providers offer calibration services for a wide range of instruments and devices used in aerospace manufacturing.
Why Calibration is a Priority for the Aviation Industry?
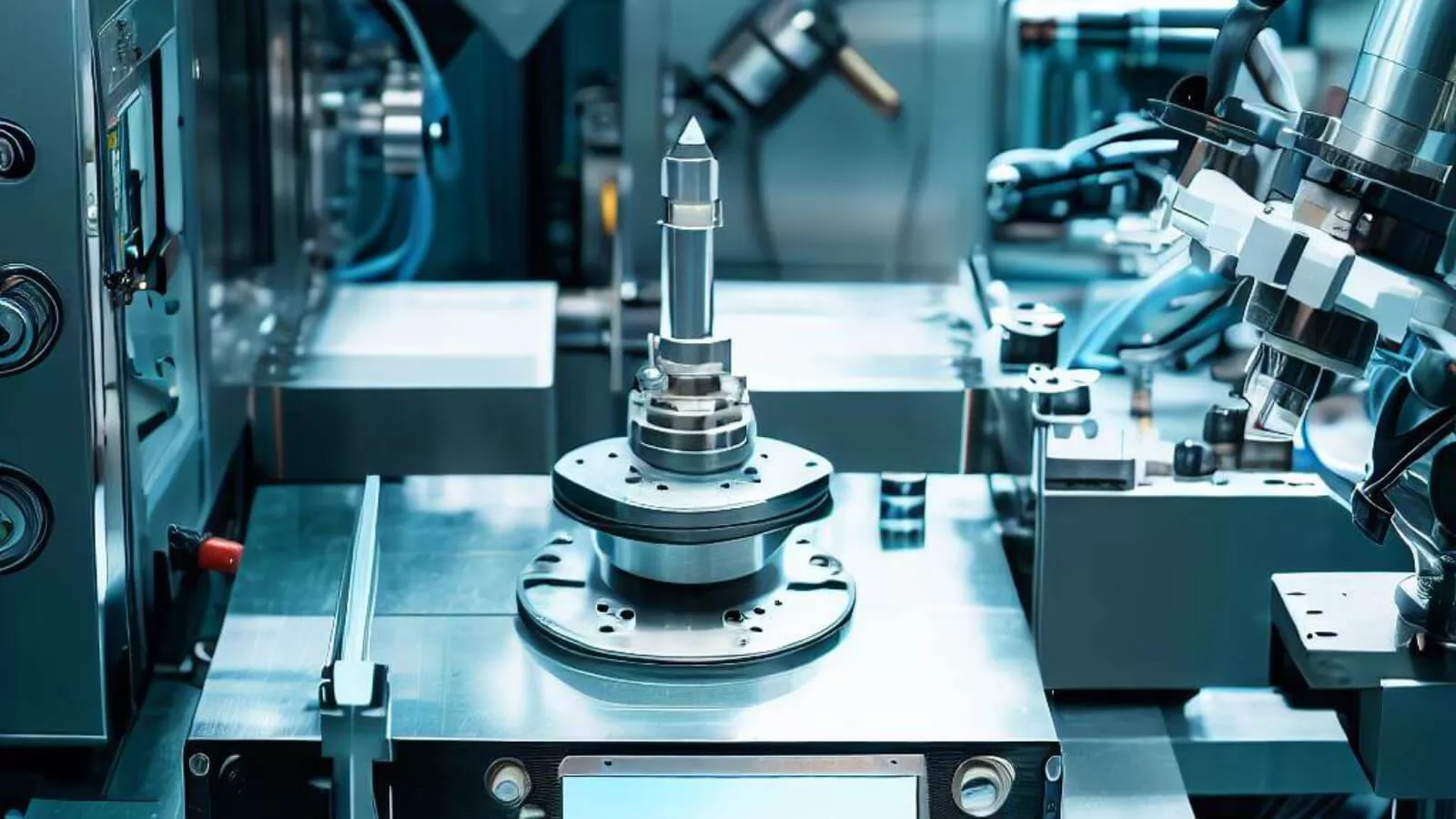
Calibration is a priority for the aviation industry for several reasons.
1. Safety and reliability of aircraft components: Calibration ensures that instruments used in aviation are accurate and reliable. This helps to reduce the risk of accidents caused by faulty instruments.
2. Regulatory compliance requirements: Aviation regulations require that instruments used in aviation are properly calibrated. Calibration certificates and documentation are required to demonstrate compliance with these regulations.
3. Maintenance and repair of aircraft equipment: properly calibrated instruments are essential for the maintenance and repair of aircraft equipment. Calibration ensures that instruments used in maintenance and repair are accurate and reliable, which helps reduce the risk of errors and defects.
Calibration equipment plays a crucial role in ensuring the safety and reliability of aircraft components in the aerospace manufacturing industry. Properly calibrated instruments are essential for maintaining the quality of aerospace components and reducing the risk of accidents caused by faulty instruments.
Calibration programs and systems are used in aviation to ensure that instruments are calibrated properly and regularly. Calibration certificates and documentation are required to demonstrate compliance with aviation regulations. Calibration services are available for aerospace manufacturers to ensure that instruments are properly calibrated.
If you want to know other information, please contact us!
Related Articles
The Ultimate Guide to Low Temperature Calibration Baths